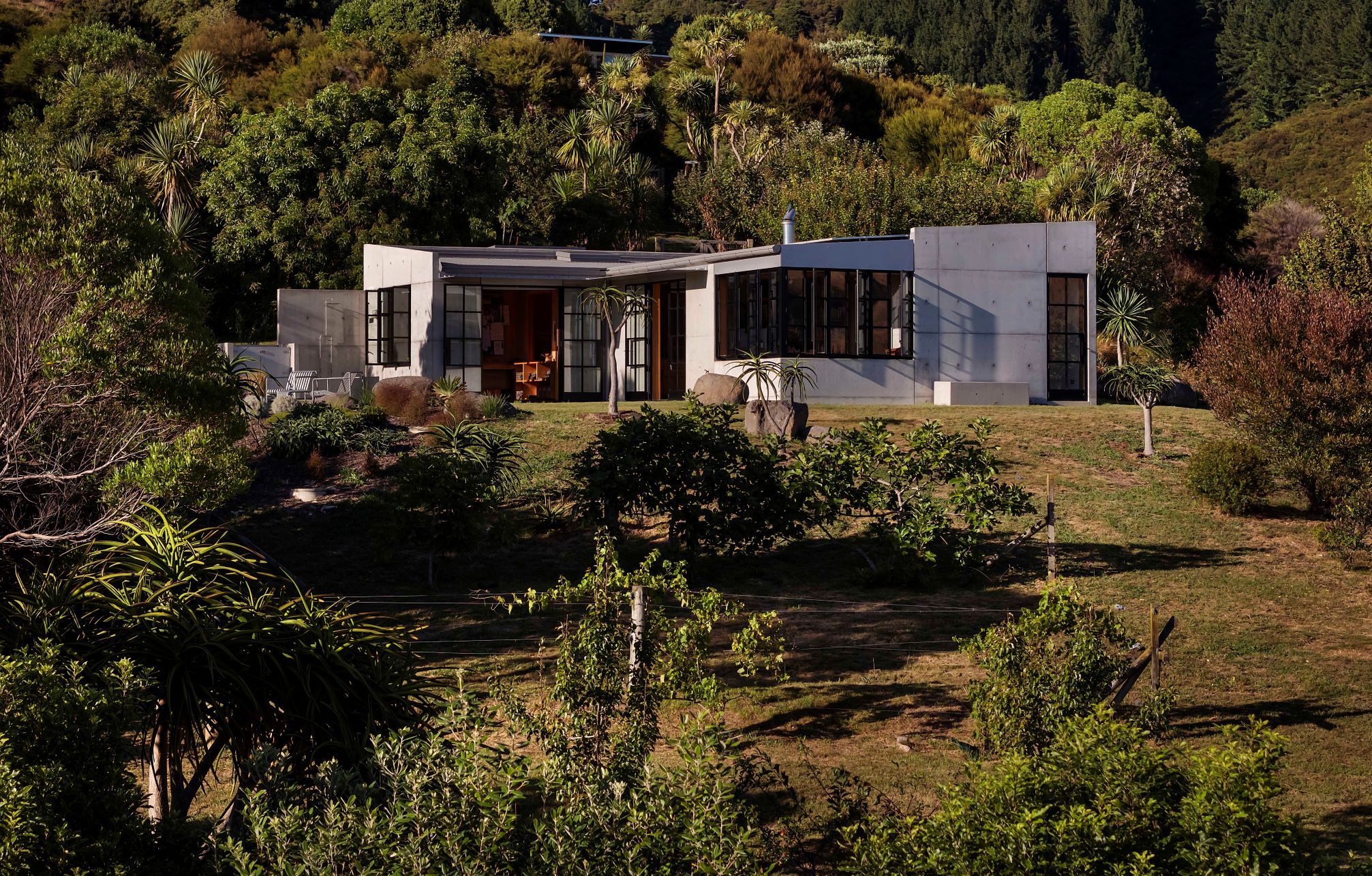
Concrete and art … a good mix for ’The Studio’
This artist's studio is a work of art in itself, sitting snuggly in amongst the bush of its rural, coastal setting at the top of the South Island. The clients, who have lived on the site for more than 20 years, called in Prue Johnstone and Mike Callaghan of Johnstone Callaghan Architects to create a new space which would connect to their existing home, accommodate their diverse art practice and cater to future requirements. This new addition was built to withstand the harsh coastal environment – making the use of insitu concrete from Firth the perfect choice!
The brief
“The client had strong ideas of a factory aesthetic using raw materials and to create spaces that would provide maximum flexibility,” says Prue Johnstone, from Johnstone Callaghan Architects. “The design was to also to include a series of raised garden-beds for an extensive vegetable garden alongside the studio. The intention was that the new studio would be enduring and ‘built to last’ – concrete and steel were the right materials to achieve the factory look the client was after.”
The clients have lived on the site for many years, carrying out extensive planting and transforming their property from its previous life as farmland, into predominantly native bush – a fabulous setting to develop a separate, standalone studio, just a short walk from their existing home.
“At the top of the section, their existing home had experienced the harsh conditions of its exposed coastal location, with ongoing maintenance issues,” adds Prue. “As such the studio (sited lower on the hill) needed to respond to this environment in a low-maintenance and durable way. A separate structure would be far more flexible, if and when they might want to downsize and move into the studio. Practically the space would need a secure office, large amounts of storage and a separate space which could function as a bedroom in the future.”
Materiality
“Insitu concrete from Firth using local Golden Bay aggregate was used for the structural and exterior skin,” says Prue. “This material has the benefit of maximum durability in the harsh coastal conditions and was used in response to the harsh coastal environment and their previous build.”
“We engaged and worked with an engineer with extensive insitu concrete experience to ensure the results. Careful coordination with the engineer, the builder and Firth was required before the pour which helped to ensure a smooth process, reduce errors and waste on site and give us the best result.”
“A concrete floor would definitely suit the desired durability while accommodating various creative practices, thermal mass benefits of the material and the overall aesthetic.”
Locally grown New Zealand Hemlock timber was used for the interior wall and ceiling linings which was paired with the more stable and refined Canadian Hemlock for the door and joinery elements. Plywood was used in the store and at the back of the house for both the wall lining and the shelving. Careful consideration of the panel layout was done with the intention to reduce waste. The metalwork elements were fabricated locally and featured a zinc arc spray protective coating.
The result
“Our client’s existing home was primarily about enjoying the sea view, so the studio was to be more inward looking and sit lower within their existing property, with low visual impact, to enjoy the hillside views to the east and glimpses of the bay to the north,” says Prue.
“The whole property and the wider environment is a really special place. The flora and fauna are amazing and, in time, we hope this studio will ‘bed in’ and be a special place to enhance one’s experience of the site.”
The Studio’s Eco features:
- The studio is fully self-sufficient with solar (a back-up generator), rainwater collection, and a septic system independent from main house.
- The combination of operable skylights and the many opening windows and doors mean that there is passive ventilation to all spaces.
- The thermal mass of insitu concrete walls and exposed concrete floor works as another passive mechanism. Large amounts of glazing allow the building to take advantage of Nelson’s sunshine hours and allow the slab to heat up.
- The timber used as the interior cladding was locally sourced New Zealand Hemlock.
Contractor: Callister Builders (Jason Callister & his team)
Architect: Johnstone Callaghan Architects
Engineer: Sullivan Hall (Fearghal McGuinness)
Concrete: Firth Self Compacting Concrete