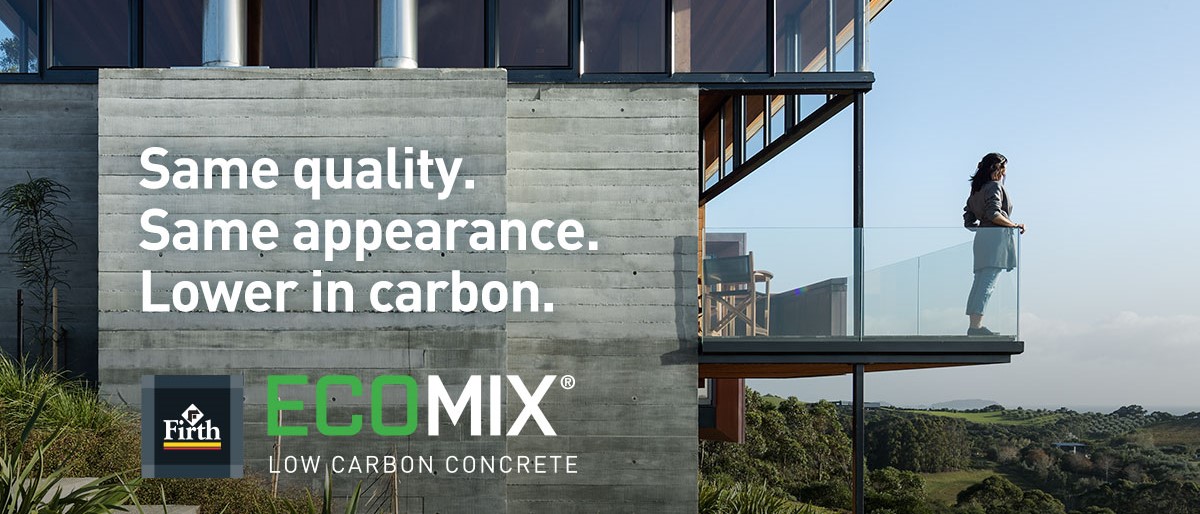
Firth EcoMix® Low Carbon Concrete – taking sustainability seriously
Designing with your carbon reduction target in mind is easy using EcoMix® Low Carbon Concrete from Firth.
Concrete is often associated with higher carbon emissions due to the large volumes used. As New Zealand’s leading concrete manufacturer Firth has been engaged in the conversation about designing low carbon concrete for many years.
Did you know that most Firth concrete is now EcoMix® Low Carbon Concrete?
“The word ‘sustainability’ is bandied around a lot but we are ‘walking the talk’ with our EcoMix® Low Carbon Concrete offering CO2 reductions from 10-50% depending on the region, local raw materials and multitude other factors which will affect the mix design,” explains Alistair Bennett, Technical Manager for Firth.
“The concrete industry is working hard to reduce carbon emissions through the use of lower carbon cements such as EcoSure from Golden Bay and Supplementary Cementitious Materials in mix designs,” says Alistair. “Although a 28-day strength is the universal specified requirement, there are a range of other attributes our technical team can specify - ie early strength, a flowable or cohesive mix - to allow placement in piles. Aggressive exposure conditions may also dictate mix ingredients. All of these requirements can have an impact on how the mix is designed, and in turn GWP of the finished concrete.”
Understanding the jargon … What is Carbon Footprint or Global Warming Potential (GWP)?
A carbon footprint is a colloquial term for the Global Warming Potential (GWP) of a material or product. It is expressed as a number of kilograms per CO2 equivalence (CO2e). The equivalence refers to converting the impact to global warming of a range of gases to that of carbon dioxide. For example, 1 kg of methane is approximately equivalent to 24 kg of CO2 in terms of global warming potential.
Claims are often made about ‘reductions in the percentage of embodied carbon’ (CO2e) - but what does this mean?
Without knowing the reference number that reduction comes from it’s impossible to know if it is the best option for reducing carbon. Instead it’s best to look for the GWP number which can be found on the product’s Environmental Product Declaration (or EPD) - a third party verified document that shows the GWP and whether it’s the right product for your project.
So, if you want lower carbon concrete, how should you specify it?
As a designer or engineer it’s important to know what strength you want for your concrete and your GWP target. Firth has developed an EC (Embodied Carbon) rating system to make specification easy. You’ll find it at MasterSpec or www.firth.co.nz.
The table below shows GWP targets for a variety of concrete strengths. When using New Zealand manufactured cement it is generally possible to achieve GWP values close to, or below, Firth’s EcoMix EC20 rating. Firth’s EcoMix EC30 and EC40 can be achieved with project specific mix designs. Designers can set the GWP and let the concrete supplier determine the most economical and safe method of achieving the targets.
We’ll do the hard work for you…
Investment by Golden Bay, New Zealand’s only cement manufacturing plant, means that the already world best practice GWP is getting lower for New Zealand-made cement. Additive and admixture technology developments are also enabling better GWP performance, and supplementary cementitious products are becoming more available.
“As a designer all you need to do is give us a call to find out what is achievable in your area to meet your client’s needs,” adds Alistair. “One of the Firth Technical Team will do the hard work for you. You can then specify the strength, GWP number and any other properties you need.”
Why concrete?
Taking a ‘whole of life’ approach to ensure the structure will be here for a long time is more important than ever, making concrete a logical choice.
Concrete's sustainability lies in its long lifespan and the potential for emissions reduction through sustainable practices.
Concrete’s benefits include:
- Long product life - with low maintenance
- Durability - perfect for foundations, retaining structures, infrastructure and industrial floors
- Fire resistant
- Good sound attenuation
- Hardscape applications (permeable mixes are achievable with additional storm water control and water quality benefits)
- Thermal mass - the ability to store heat providing inertia against temperature fluctuations.
- Carbonation – concrete absorbs atmospheric CO2
These benefits, combined with availability, excellent quality control and cost competitiveness make concrete construction an attractive proposition as the industry, and market leaders like Firth, are continually working on ways to reduce the carbon footprint of concrete.
It is possible to build with concrete and reduce your carbon footprint - and Firth is here to help you do it. Go to firth.co.nz or call us on 0800FIRTH1 for help.