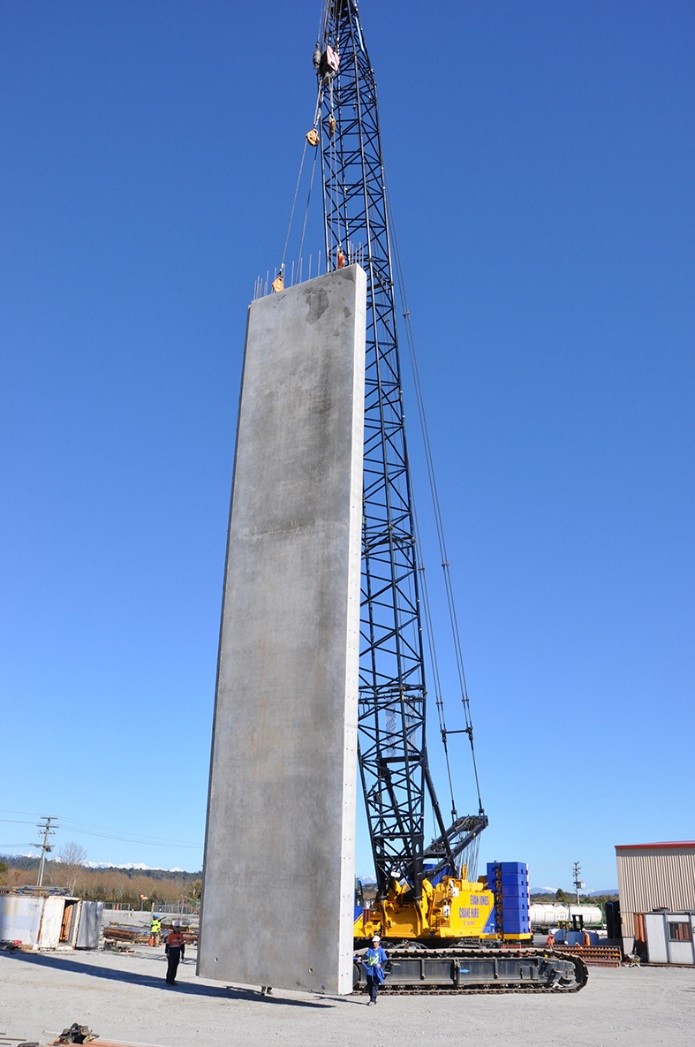
Whilst it’s been a tough few years on the West Coast for the work force and economy with the closure of several high profile mines, a bright spot for the local construction industry has been the decision by Westland Milk Products to build a new nutritionals dryer at the dairy cooperative’s site in Hokitika.
The construction of the new dryer has been welcomed by local construction company Evan Jones Construction, the main contractor, and sub contractors Firth, who have been busy producing concrete for the past few months for the large precast structure.
“There have been a few large pours for the pre-cast panels that Evan Jones Construction are manufacturing,” says Steve Kelly, Plant Manager at Greymouth for Firth. “These panels are being poured two at a time in panel beds. They require reasonably high strength mixes with 40MPa for the main panels and 45MPa for the wings. Each of the panels needs to cure to about 35MPa, which takes about three weeks, before they can be lifted. This is impressive to watch as these things are 24m long and weigh 98.7 tonnes each!”
With construction less than half way through, Evan Jones, Director of Evan Jones Construction, is happy with progress. “We have built most of the factory for Westland Dairy on this site over the years and have a good relationship with them. They know us well and know we can do the job for them. We have also had a 27-year long relationship with Firth. We need to rely on our suppliers and I have always been able to rely on Firth. In fact we have extended this relationship to a supply contract for our company in Blenheim who is also using Firth.”
The construction of the $102 million purpose-built spray drier, referred to as D7 – which also includes new batching equipment, high specification mixing equipment, additional warehousing, another laboratory and packing line – began in April and has involved the supply of large volumes of concrete by Firth, for the manufacture of very large and extremely heavy precast panels.
With five of the eight 24m panels completed and with two slightly smaller and then another eight 11m long panels still required, there is still a bit of work to do to complete the new dryer facility.
“This is the biggest job we have had on the coast for a number of years,” says Steve. “It came at a good time.”