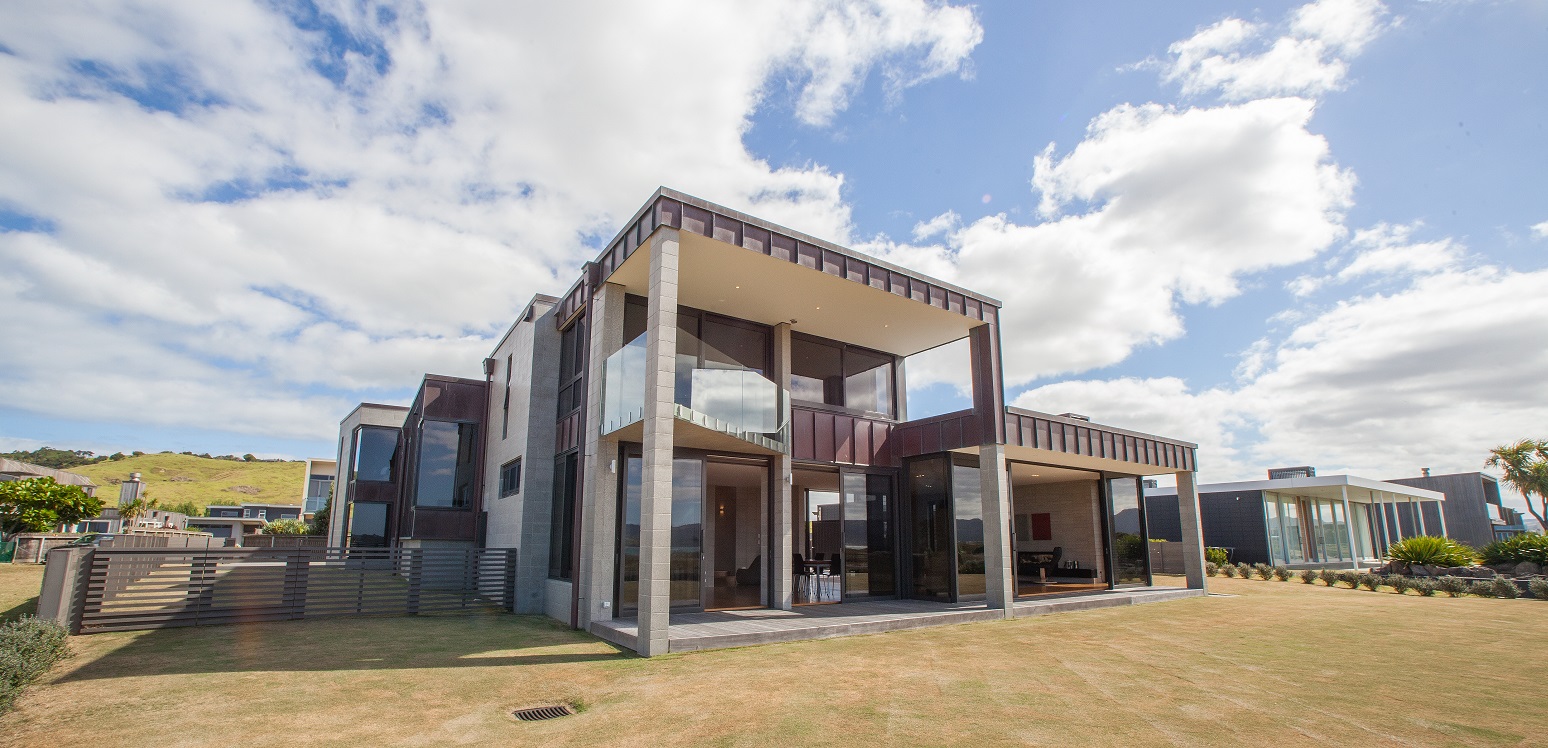
Firth's 10 series Grey Masonry has been used on the impressive double storey home as a veneer for the exterior walls of the house with a 50mm cavity between the veneer and Firth’s 20 series structural HotBloc. The double skin block design was developed to ensure the house was not only well insulated, watertight and durable - to suit the coastal location - but to also achieve the look the homeowners were after.
Grant Neill, now a Director of Pacific Environments NZ Ltd and the architect commissioned to design the house, explains. “Owners Brent and Debbie Forman were adamant from the start that the main components of the house had to be copper, concrete and glass. The brief they gave me was that they wanted the house to be strong and it had to suit the environment. The intention was to always have a honed, stack bonded exterior block cladding, but to ensure that there would never be issues with water tightness in this coastal location, I designed the internal structural walls to also be in block, and to keep the look consistent from the inside to the outside.”
The 50mm cavity between the block walls and the inbuilt polystyrene insulation of Firth’s HotBloc means the house is extremely well insulted - achieving the best possible R-Values. Click here for the Building Code definition of R-Value. “A single block external wall with an internal exposed finish may not have offered the water tightness and insulation that this system provides,” adds Grant.
Brent and Debbie entrusted the construction of their new beach side home to Brackenridge Builders – a local Warkworth company with 25 years experience in the area. Construction Manager, Tony Borich, talks about the process. “This is the first time we have used this construction method and I have to say that it is very effective, resulting in an extremely watertight and well insulated dwelling. The honed, diamond ground finish of both the exterior and interior walls looks great. We used very skilled subcontractors, local block layer in Dean Watson and Phil Gerring from BlockTec, completed the look by honing and polishing the blocks.
The entrance to the house features a gently curved block wall which, once honed, exposed the pumice in the block, resulting in a soft grey finish. “Although ‘gutsy’ materials were used I am happy to say that the overall feel of the house is quite soft and light. The timber floors and the soft grey of the exposed walls, including the 10 series feature wall in the lounge, have worked extremely well together,” said Grant.
The internal block walls offer thermal mass properties ensuring energy and financial savings as well as the added benefit of a moderate, comfortable internal temperature for the owners. By taking advantage of concrete's thermal mass, in combination with good insulation and glazing, the masonry walls will regulate internal temperatures to provide a healthy and energy efficient living environment throughout the year.
Grant says that this type of design is not as costly as homeowners might think. “We compared the cost of this build to the m2 rate of other builds in Omaha and they are comparable. So it’s not as expensive as you might first think. I think it’s been a very successful project for everyone concerned.”
“It is an exciting, interesting and different home to live in,” says Brent. “Grant did a great job in following our brief. The house is also proving very durable and energy efficient.”
“I love the internal block walls,” adds Debbie.
“They are almost silky to touch. We are very happy.”
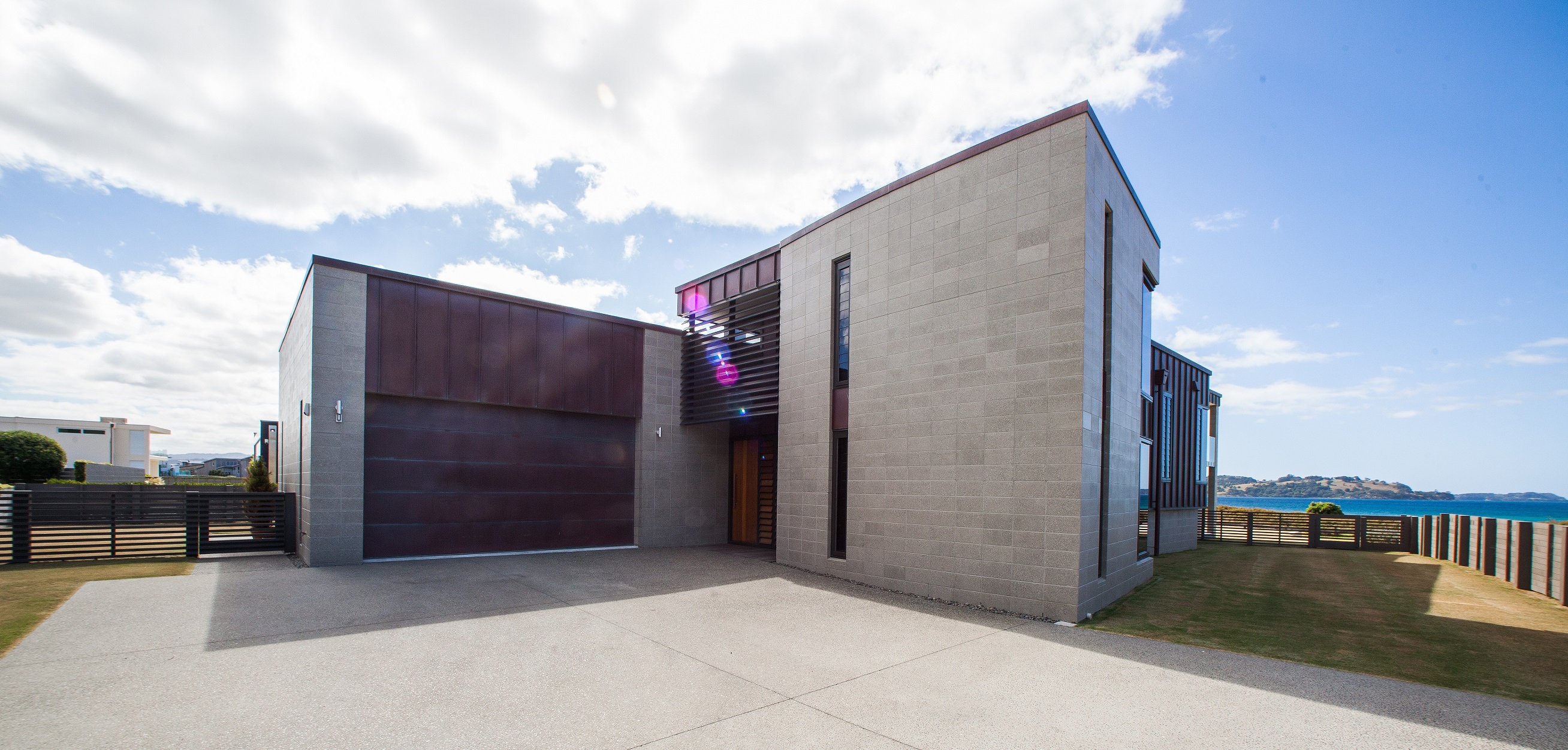
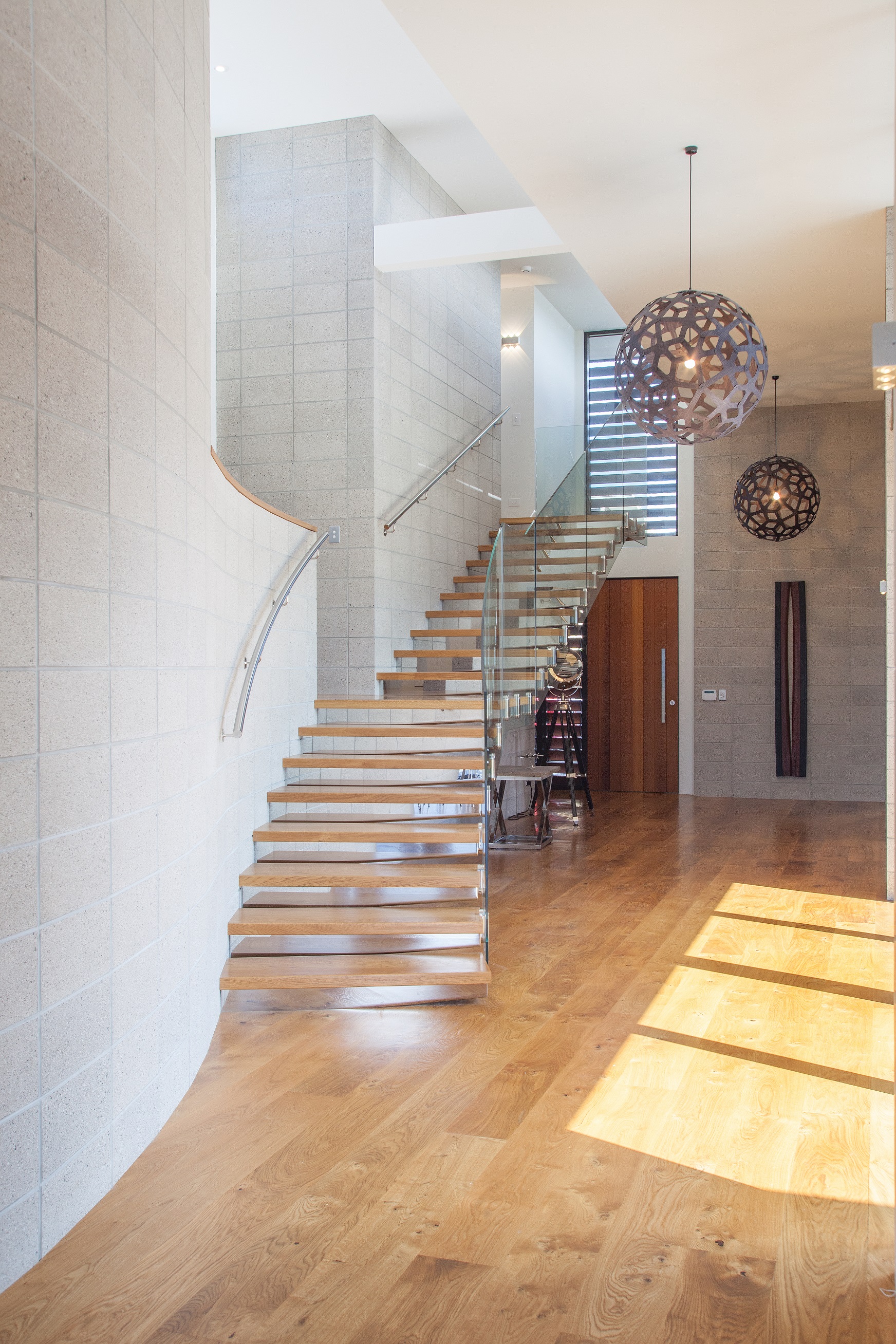